The Single 12V Rail SilverStone Olympia OP650
by Christoph Katzer on July 13, 2007 12:00 PM EST- Posted in
- Cases/Cooling/PSUs
The Inside
After opening the housing we are presented with a very clean and systematic arrangement of components. Firstly, the two big heatsinks reveal the first signs of the old Etasis crew. In the most recent designs from Etasis, we find power supplies built with two printed circuit boards that still fit into a standard sized housing. This was made possible through the selection of components which are very short.

The same is clearly visible on first sight in our Silverstone Olympia power supply. Where other manufacturers are using a big capacitor on the primary section, Silverstone designed their PSU using three smaller ones to fit under the massive heatsink. The second difference to most other power supplies is that there are three transformers in the middle of the PCB. Normally this is implemented with one big transformer used to generate all outputs to the PC and a smaller transformer to generate the 5v stand-by rail.
Filtering stage
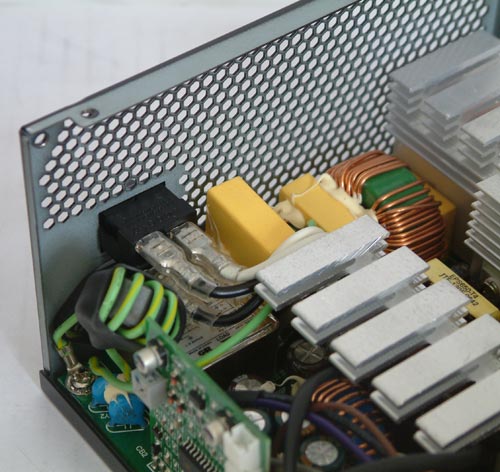
The filtering stage is taken really seriously in the OP650. We found an EMI-filter which is basically there to prevent interferences from the power supply going back into the AC source. The three yellow blocks between the ferrite coils are called X-capacitors and the Y-caps are positioned on the far right side under the heatsinks. Beside this is the rectifier bridge which converts the alternating current into direct current. Silverstone placed it direct on the primary heatsink in order to help dissipate the heat generated by the rectifier.
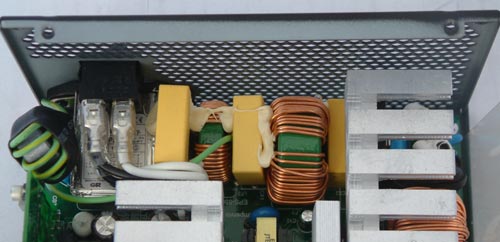
After opening the housing we are presented with a very clean and systematic arrangement of components. Firstly, the two big heatsinks reveal the first signs of the old Etasis crew. In the most recent designs from Etasis, we find power supplies built with two printed circuit boards that still fit into a standard sized housing. This was made possible through the selection of components which are very short.

The same is clearly visible on first sight in our Silverstone Olympia power supply. Where other manufacturers are using a big capacitor on the primary section, Silverstone designed their PSU using three smaller ones to fit under the massive heatsink. The second difference to most other power supplies is that there are three transformers in the middle of the PCB. Normally this is implemented with one big transformer used to generate all outputs to the PC and a smaller transformer to generate the 5v stand-by rail.
Filtering stage
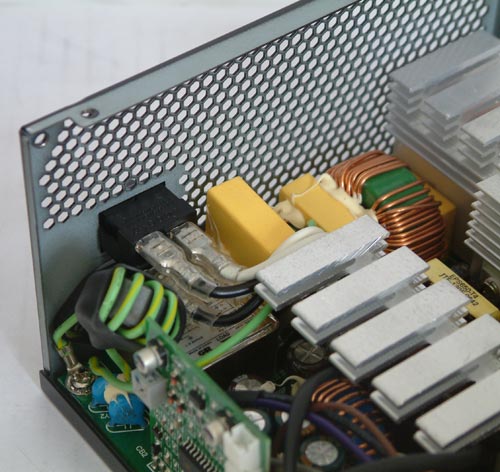
The filtering stage is taken really seriously in the OP650. We found an EMI-filter which is basically there to prevent interferences from the power supply going back into the AC source. The three yellow blocks between the ferrite coils are called X-capacitors and the Y-caps are positioned on the far right side under the heatsinks. Beside this is the rectifier bridge which converts the alternating current into direct current. Silverstone placed it direct on the primary heatsink in order to help dissipate the heat generated by the rectifier.
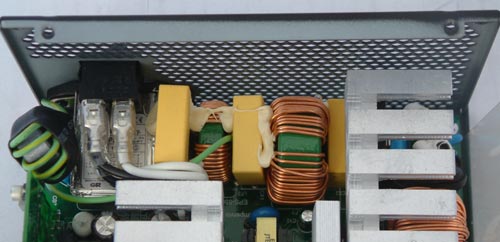
46 Comments
View All Comments
YellowWing - Friday, July 13, 2007 - link
In a prior article you showed us the box you use for testing power supplies. I don't remember reading how the heat generated by the power supplies is removed from the sealed box. Does the temp of the air in the box rise with time? Would the drop off in voltage be less with full ventilation?YellowWing - Friday, July 13, 2007 - link
Brownouts have caused power supply failures for me in the past. How about dialing the input voltage down to 90 or so and see what happens.From experience I can say that some supplies don't survive at lower input voltages.
DerekWilson - Friday, July 13, 2007 - link
we are considering looking at 90V input. Thanks for the suggestion.bpt8056 - Friday, July 13, 2007 - link
I just want to say that I thought AT did a great job on the review. Keep up the great work!puffpio - Friday, July 13, 2007 - link
Great article..looking forward to many many moreOn one of the graphs of the 230V tests, it is labeled as 115V
jonnyGURU - Friday, July 13, 2007 - link
Good job. Clearly a lot of effort was put behind putting the methodology and this review together.Couple questions..
1. How much of the voltage drop shown would you contribute to the resistance created by the interface board and wires located between the end of the PSU's connector and the actual load. This isn't my favorite power supply, but I know the voltage regulation isn't nearly as bad as you have it graphed. And naturallly, since load also creates resistance, your voltage is going to decrease exponentially if you're not loading and measuring at the end of the connector. Since you're using a Chroma, I know you're not loading and measuring at the connector. Perhaps you could rig a DMM to measure voltages at the end of the connector instead of reporting what the Chroma is telling you since the Chroma is going to be incorrect since it doesn't take into consideration this added resistance.
2. Do you think it's possible to define "10%, 20%, etc." as it pertains to your loads. Naturally, you can't load all rails by 80%, 90%, 100%" because you'd easily exceed the power supplies capabilities. And certainly you're not loading the +12V with 80%, 90% 100% and then filling up the remainder with a 3.3V and 5V load because then you would crossload the PSU with an unusually high +12V load.
3. And, at risk of sounding like I'm beating a dead horse, ripple and noise results. We all know spec is 1%, and ripple and noise does typically increase with load. It would be nice to see if the power supplies being tested stay within that spec. through out it's total advertised capability.
Thanks and I look forward to the next PSU review!
mcvan - Saturday, July 14, 2007 - link
Like Johnny said. ;)Another issue pertinent to the extreme sag in voltage lines and perhaps to the soaring temperatures is to ask how long the PSU was run at each load level (and in total) and what was the air temperature at the PSU intake? Maybe the test box is just letting the PSU get way too unnaturally hot, and this has a deleterious effect on performance. This test box is not the same as thermal control chamber where you can dial in a specific target temperature, which will then be held constant by the chamber throughout the testing.
Since the test box is well insulated and sealed, there is a direct correlation between time spent with the PSU on and internal air temperature. No matter how the PSU is cooled, at any load, the temperature of the test box should rise continuously (even if only incrementally at very low load) as long as the PSU is running. This is a significant uncontrolled and unreported factor. That PSU intake temperature will be dictated by a complex mix of factors, by too many variables --
-starting ambient air temp in the box
-how long the PSU is kept running in the box and at which loads
-heat loss out of the box
-efficiency curve of the PSU
-fan and fan controller characteristics
If the time spent at each load and the starting ambient temp is kept the same for each and all PSUs, then the variables are correctly contained to the PSUs being tested. Then differences in the air temperature at the intake at any given power level for each PSU would reflect real differences in the cooling system and efficiency of each PSU. It would ensure a more level thermal playing field.
qpwoei - Friday, July 13, 2007 - link
While we're beating dead horses, I'll land a few blows on the dynamic load response horse as well :)
SilthDraeth - Friday, July 13, 2007 - link
Seems like you know what you are talking about. I hope they take some of your points into consideration, since they all seem very valid.jonnyGURU - Friday, July 13, 2007 - link
Thanks. But I'm just an old hack. ;)