Cooler Master Silent Pro PSUs
by Christoph Katzer on September 8, 2008 3:00 AM EST- Posted in
- Cases/Cooling/PSUs
Efficiency and PFC
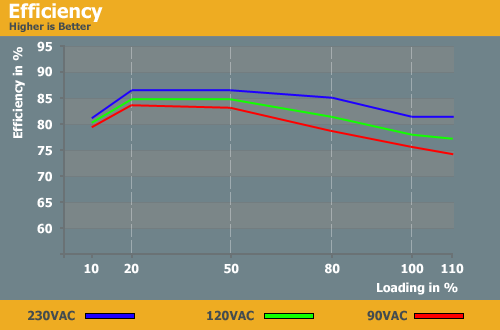
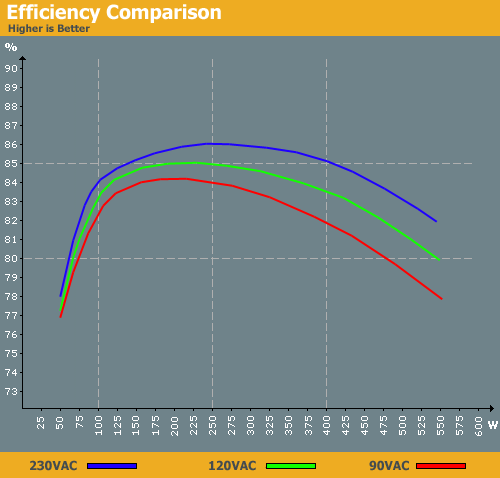
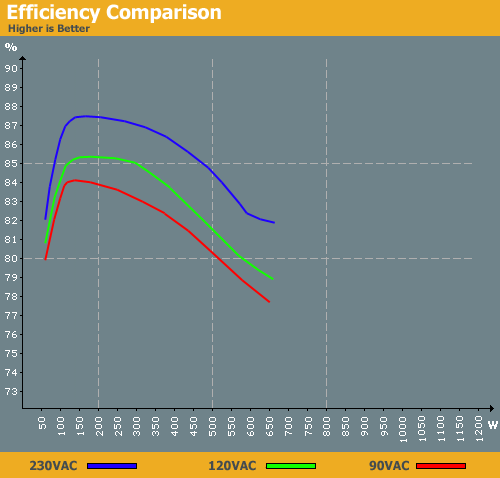
The efficiency is good, and with 230VAC it stays above 82% throughout testing. The maximum of 87% efficiency of the 600W unit is better than the 500W model, which only makes it up to 86%. Given the nearly identical design, we were a little surprised to see any differences at all in the efficiency curves. The 500W curves look similar to what we normally see, but the 600W unit is a little odd. It performs extremely well in the first half of the output curve, from a low input of 130W to 400W, but then it drops rapidly and eventually falls into the sub-80% range with 120VAC/90VAC. Normally, we don't see efficiency drop much lower than the initial values. The 600W model still performs better than the 500W unit overall, but it runs optimally in the 130W to ~350W range.
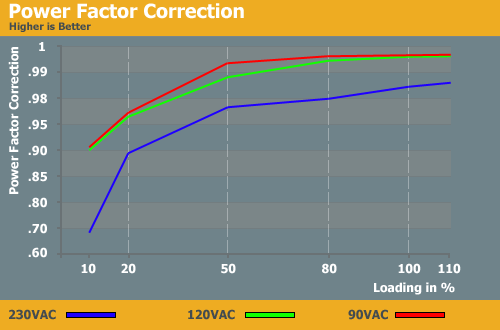
The power factor correction is also a little strange, since it starts at a really low value and stays lower than normal with 230VAC. Lower input voltage means better PFC and the result improves, getting close to .994 which is not bad.
15 Comments
View All Comments
Megaknight - Tuesday, September 9, 2008 - link
And once again the american consumer is screwed by stupid companies and the stupid US patent system...Amart - Monday, September 8, 2008 - link
The Ripple/Noise charts and a dedicated page for Quality are a good decision - thank you.OverDraught - Monday, September 8, 2008 - link
The product label does not show the UL mark, which has probably been applied for but not issued yet. No big deal unless you are in the USA and are building computers for resale or lease. If so, check with your product liability carrier before using this product.Personally, I would never by a PSU that was not UL listed.
JarredWalton - Monday, September 8, 2008 - link
As stated, the patent issues are keeping this out of the US for now, so the lack of a UL mark might have something to do with that. If/when that's resolved, then we can see if the UL is listed.Bozo Galora - Monday, September 8, 2008 - link
Well, I feel like I was just struck by lightning.Actual ripple graphs within an AT PSU review.
Beat me with a giant wet Ramen noodle.
(Anyone see pigs flying?)
semo - Monday, September 8, 2008 - link
"Cooler Master advertises their use of small copper plates on the heatsinks as a means of increasing heat dissipation, since copper transfers heat faster than aluminum. Aluminum still dissipates the heat faster to the surrounding air"so both aluminum and copper dissipate heat faster... compared to what?
also why isn't there any comarison to other psus. For example the sample reviewed here is more expansive than the CoolerMaster 520W Real Power Pro Modular but does it deserve the 50% mark up in price?
Christoph Katzer - Monday, September 8, 2008 - link
huh? yeah...Heat goes faster through copper than through aluminum. But aluminum can dissipate the heat faster into the air. This is why we have today mostly aluminum-coolers with a copper base which Cooler Master used for these power supplies now...
We do regular comparisons with the Buyer's Guide and sometimes in roundups.
For starters your mentioned unit comes from Acbel and is not even half as tough as an Enhance-build PSU like the Silentpro.
Howard - Monday, September 8, 2008 - link
I don't believe that aluminum dissipates heat faster than copper does. The reason why we have heatsinks that are a mix is probably because aluminum is much cheaper (and lighter, though that is probably a secondary rather than primary factor).bludragon - Monday, September 8, 2008 - link
I agree. I think we need mythbusters on this one. Cu has higher conductivity than Al. But, Cu is heavier, more expensive and harder to machine so we reach the compromise of Cu base and Al fins.PEJUman - Monday, September 8, 2008 - link
It's true Cu retains heat better than Al.Here are the simple clues:
Cu have higher conductivity and Specific heat than Al.
Conduction (CPU/Transistor to heatsink) needs good thermal conductivity.
Convection (Heat sink's fins to ambient air) needs a lot of surface area.
simple explaination:
While with higher conductivity, Cu will transport heat faster, but with the higher spec. heat Cu will stores more energy than Al (at the same shape and volume) while having the same surface area, thus Cu will be harder to dissipate convectively.
Now the long explaination:
Copper is a good candidate as first line 'heat sink', it will absorb a lot of energy before increasing 1 deg, meaning for a CPU at 47 deg and ambient at 27 deg, it will hold 27... 28... 29... 30 deg longer than Al as it heats up. - GOOD
now comes the drawback, with the high specific heat, when copper try to release heat to ambient air, it will maintain it's hot temperature longer than Aluminum simply because it has to dissipate more energy to ambient air before dropping 1 deg in temp.
So, let's imagine copper fins with the same shape and volume as Al, it will take a lot more air to cool the copper (not to mention it's heavier too) than the Al. - BAD
Thus the reason using Al for fins, and copper for heat block (sink).
asborbing heat from transistor or CPU got to do with small contact surface area, in which case higher thermal conductivity allows lower interface junction temp). while the Al fins dissipate heat more efficiently (in terms of heat flux/weight/size) than cooper.
Now, heat sink is just like any other overclocking quest, you're bound by the weakest link. Thus to come up with a good heatsink assembly you need to have properly sized Cu sink & Al fin.
This means sufficient surface area between the Al & Cu interface to sustain the same heat flux rate that the Cu is capable to aborb and Al fins capable to dissipate.
Mess this balance up, and your again bound by your weakest link, be it your copper block, Al fins of its Cu-Al interface area.